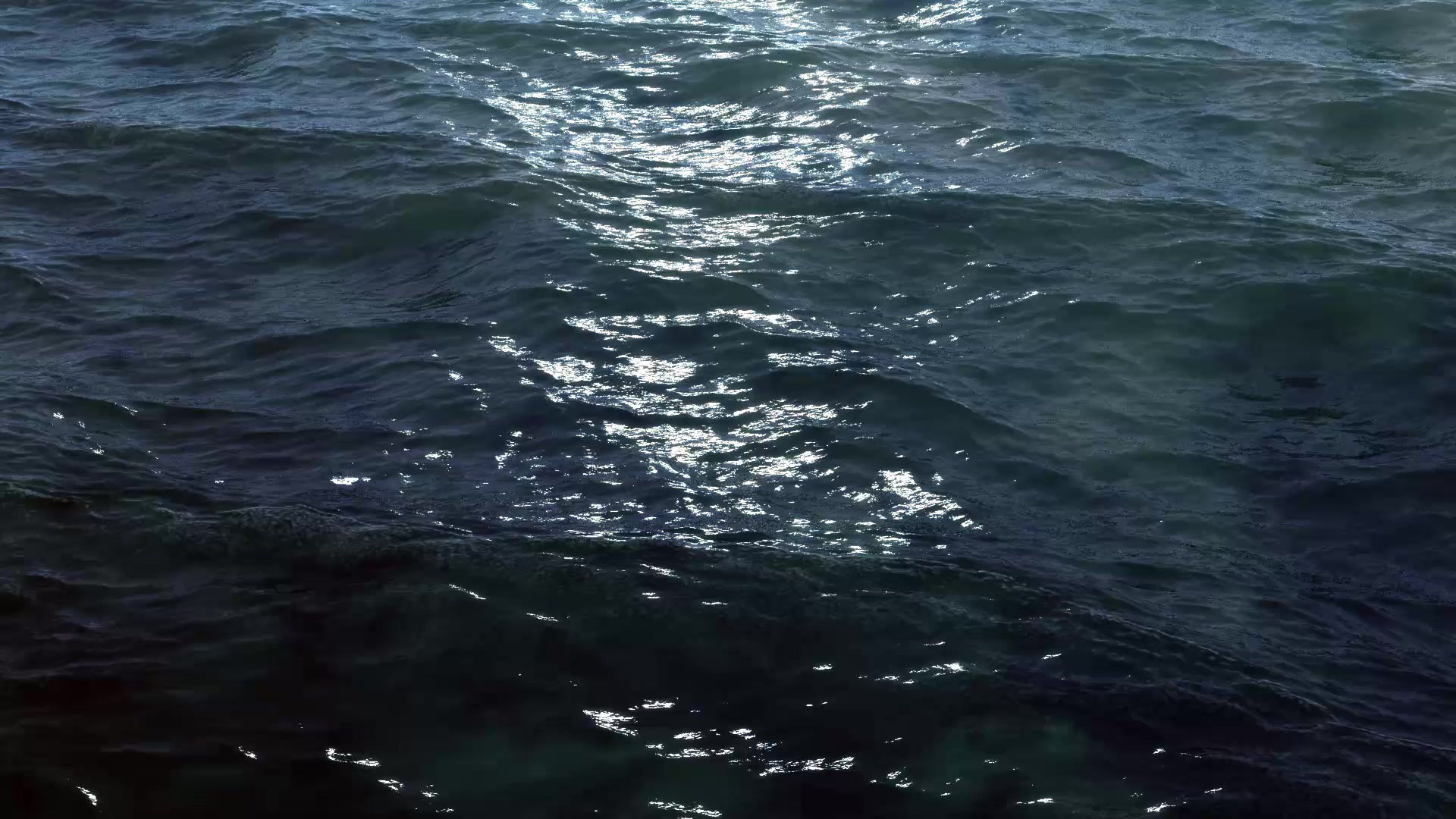
THE WINDSOR CONSULTING GROUP, INC.
Certified Industrial Hygienists and Safety Professionals
Hazard Operations (HAZOP)
What is HAZOP?
It is a systematic risk technique to identify potential HAZard and OPerating problems.A formal systematic rigorous examination to the process and engineering facets of a production facility.A qualitative technique based on“guide-words”to help provoke thoughts about the way deviations from the intended operating conditions can lead to hazardous situations or operability problems HAZOP is basically for safety -Hazards are the main concern -Operability problems degrade plant performance(product quality, production rate,profit) Considerable engineering insight is required-engineers working independently could develop different result.
Objective of HAZOP:
-
For identifying cause and the consequences of perceived mal operations of equipment and associated operator interfaces in the context of the complete system.
-
It accommodates the status of recognized design standards and codes of practice but rightly questions the relevance of these in specific circumstances where hazards may remain undetected.
How and Why HAZOP is Used:
-
HAZOP identifies potential hazards,failures and operability problems.
-
Its use is recommended as a principal method by professional institutions and legislators on the basis of proven capabilities for over 40 years.
-
It is most effective as a team effort consists of plant and designers,operating personnel,control and instrumentation engineer etc.
-
It encourages creativity in design concept evaluation.
-
Its use results in fewer commissioning and operational problems and better informed personnel,thus confirming overall cost effectiveness improvement.
-
Necessary changes to a system for eliminating or reducing the probability of operating deviations are suggested by the analytical procedure.
-
HAZOP provides a necessary management tool and bonus in so far that it demonstrates to insurers and inspect or evidence of comprehensive thoroughness.
-
HAZOP reports are an integral part of plant and safety records and are also applicable to design changes and plant modifications, there by containing accountability for equipment and its associated human interface throughout the operating life time.
-
HAZOP technique is now used by most major companies handling and processing hazardous material,especially those where engineering practice involves elevated operating parameters:
- oil and gas production
- flammable and toxicchemicals
- pharmaceuticals etc.,
-
Progressive legislation in encouraging smaller and specialty manufacturing sites to adopt the method also as standard practice.
Six Steps in the HAZOP Process:
-
Project exploration/preliminary project assessment to identify inherent hazards of process chemicals,site suitability and probable environmental impact.
-
Project definition to identify and reduce significant hazards associated with items and areas,check conformity with relevant standards and codes of practices.
-
Design and procurement–to examine the PID in detail for identification of deviations from design intent capable of causing operability problems or hazards.
-
During final stages of construction–to check that all recommended and accepted actions recorded in steps 1-3 implemented.
-
During plant commissioning–to check that all relevant statutory requirements have been acknowledges and all installed safety systems are reliably operable.
-
During normal operation, sometime after start up especially if any modification been made.Tocheck if changes in operation has not invalidated the HAZOP report of step iii by introducing new hazards.